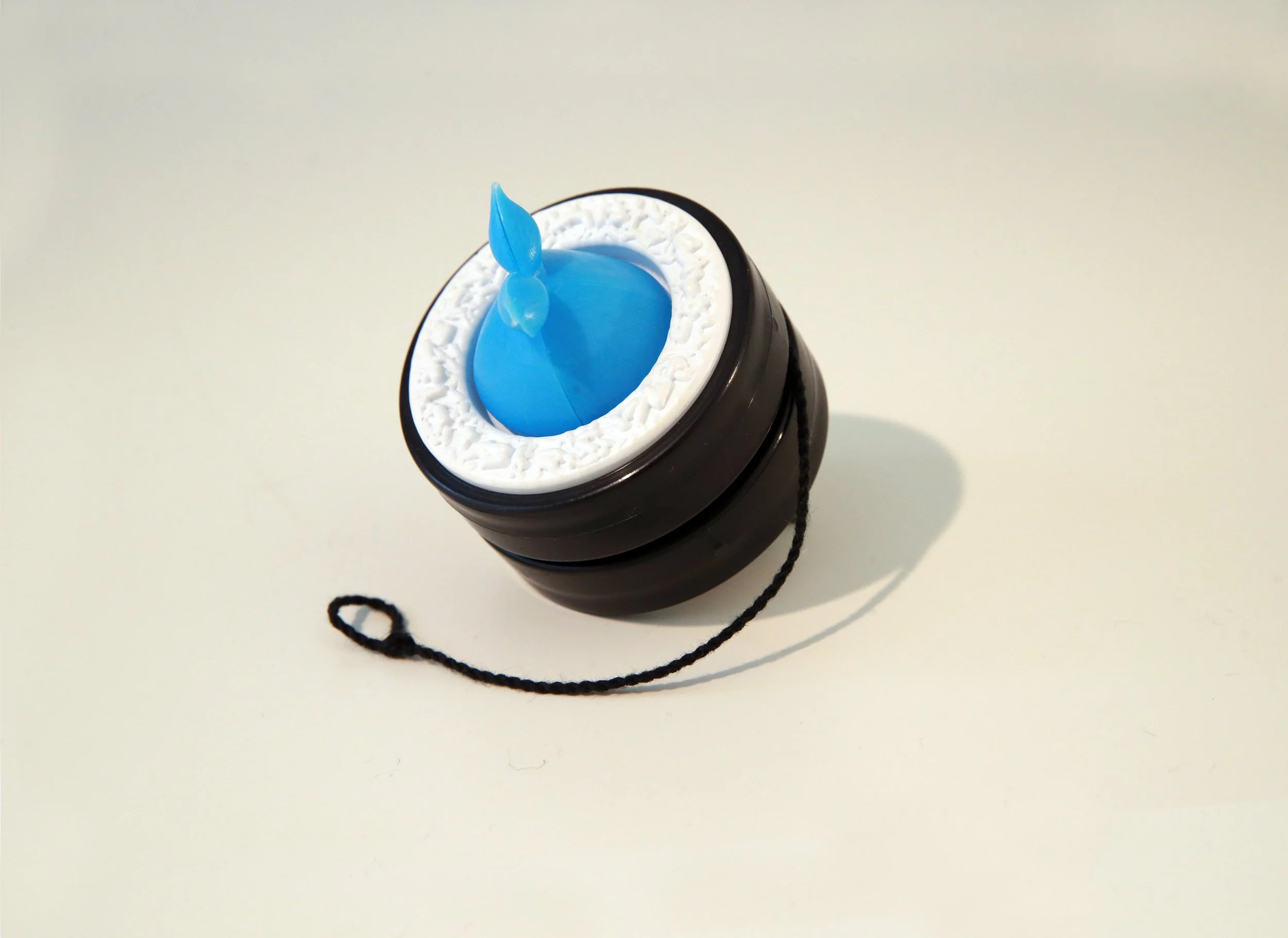
yo-yo
Manufacturing Study, Yo-yo
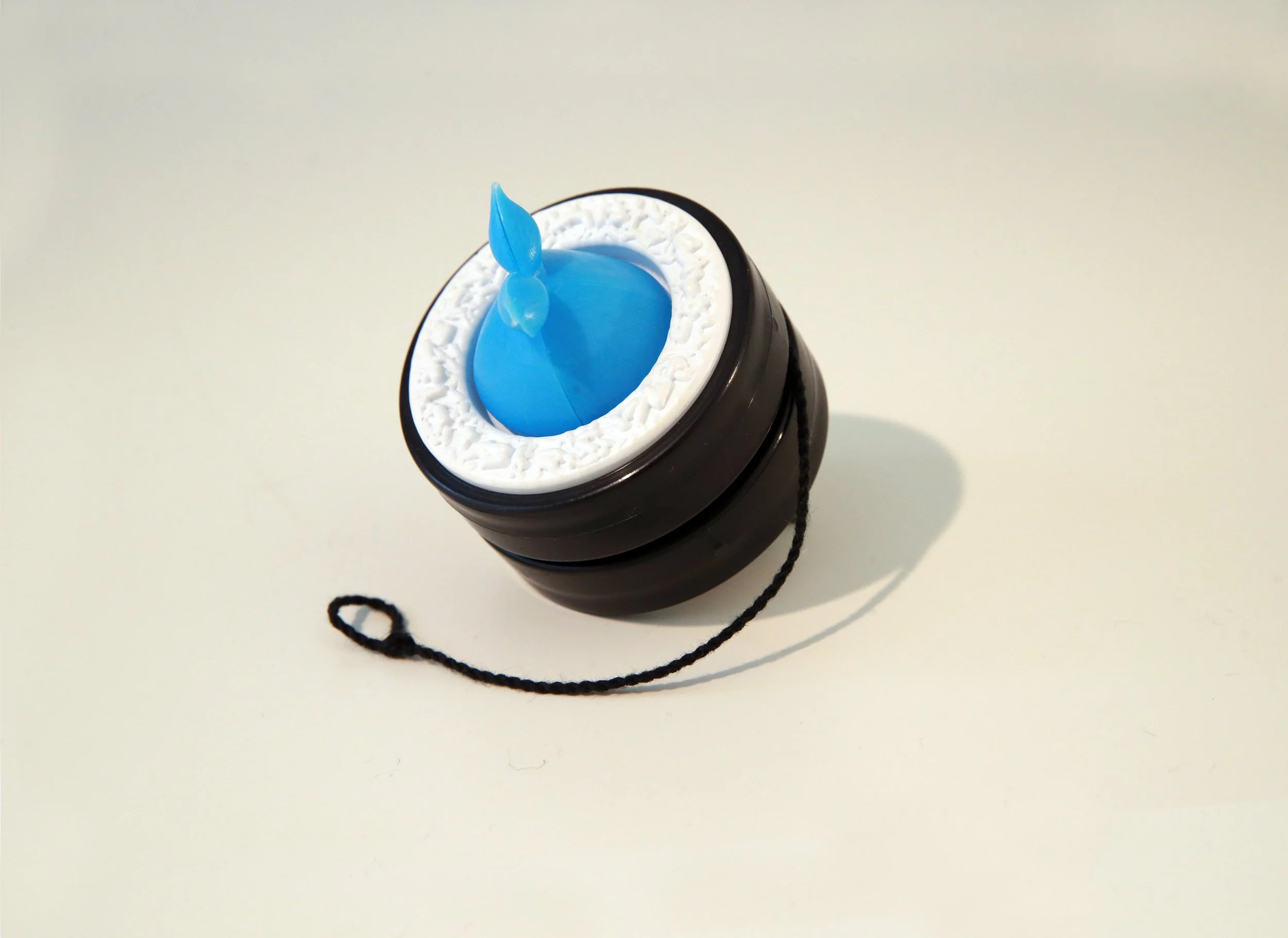

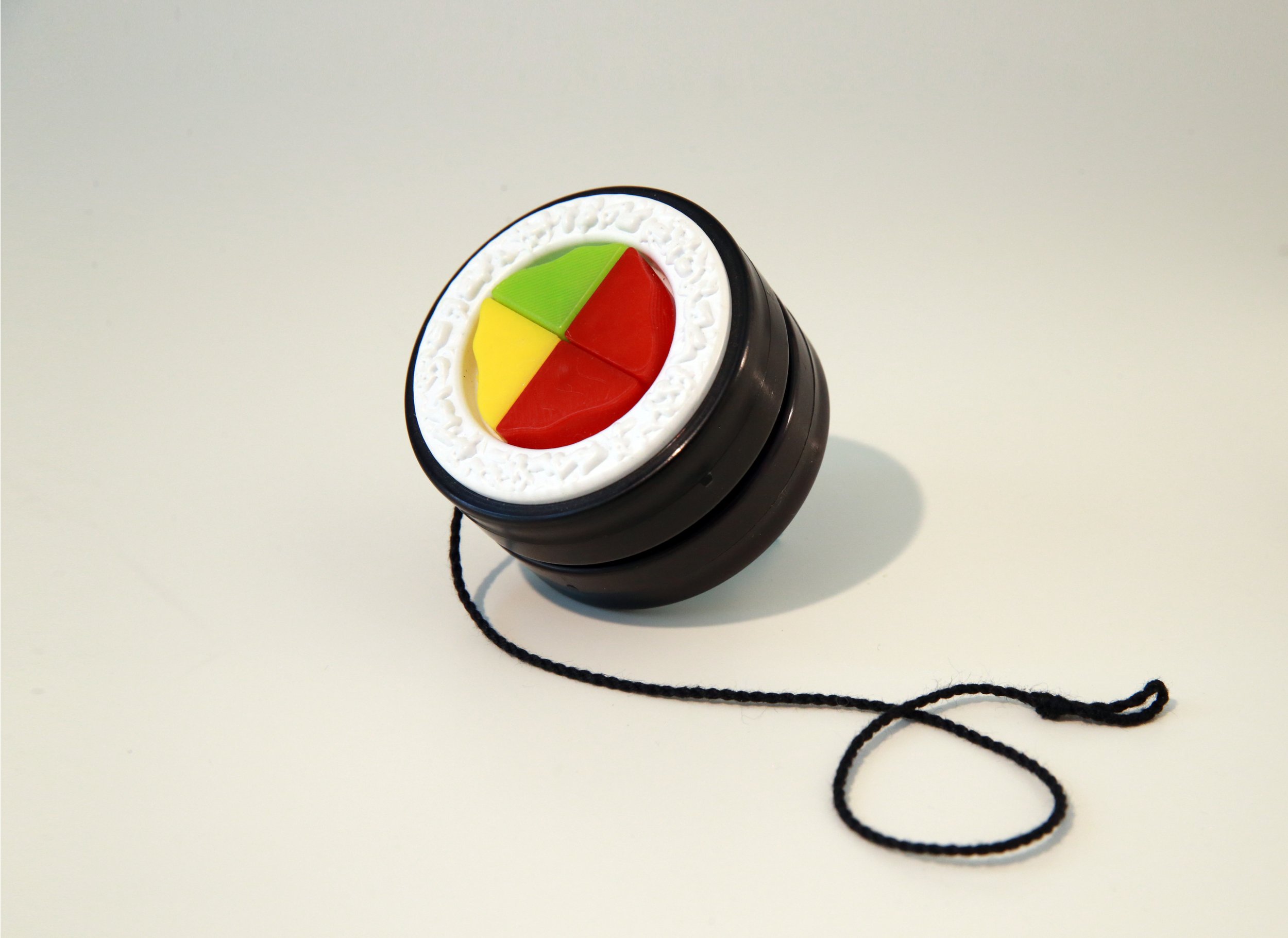
YOYOMATO
Fall 2016
2.008 - Design and Manufacturing II @MIT
Skills Developed — ideation, tolerance and critical dimension analysis, mold design and fabrication, thermoforming, injection molding, process monitoring, cost analysis, project scheduling
Materials / Processes — injection molded and thermoformed plastic, steel shims
Documentation — process blog, paper, poster (below)
In small teams of six, we designed, developed, and "mass" produced a custom yoyo. Our team Yoyomato, named after a local sushi buffet, designed a sushi-inspired yoyo. The yoyo contains sushi fillings, a fish tail, rice, a seaweed base, and metal shims.
Taking inspiration from shrimp nigiri, a unique element of our yo-yo is its asymmetry. However, this shifted the yo-yos center of gravity, causing wobbling during use. Weighted shims were embedded into the yoyo base to provide balance and enough mass for a smooth play experience. The sushi fillings, fish tail, and the base were injection molded while the rice was thermoformed. The injection molds were machined from aluminum since our production was low-volume (<200 parts per mold). In order to achieve the detailed texture of the rice, the thermoforming mold was SLA 3D printed. I focused on the rice component, printing and iterating the mold design for panelization density and cosmetics, and optimizing the thermoforming parameters. To evaluate the designs and manufacturing methods, we tracked critical dimensions to evaluate manufacturing distributions and calculated expected yields.
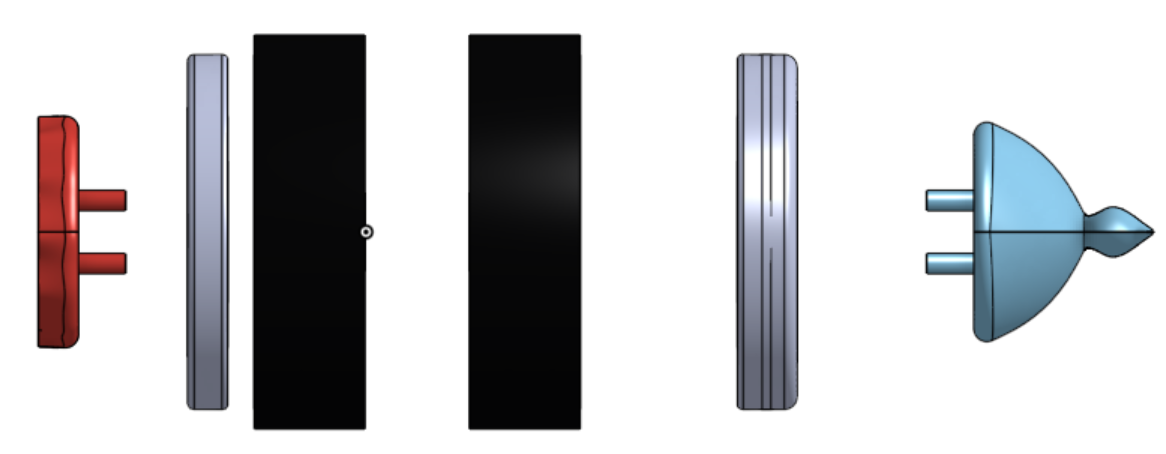

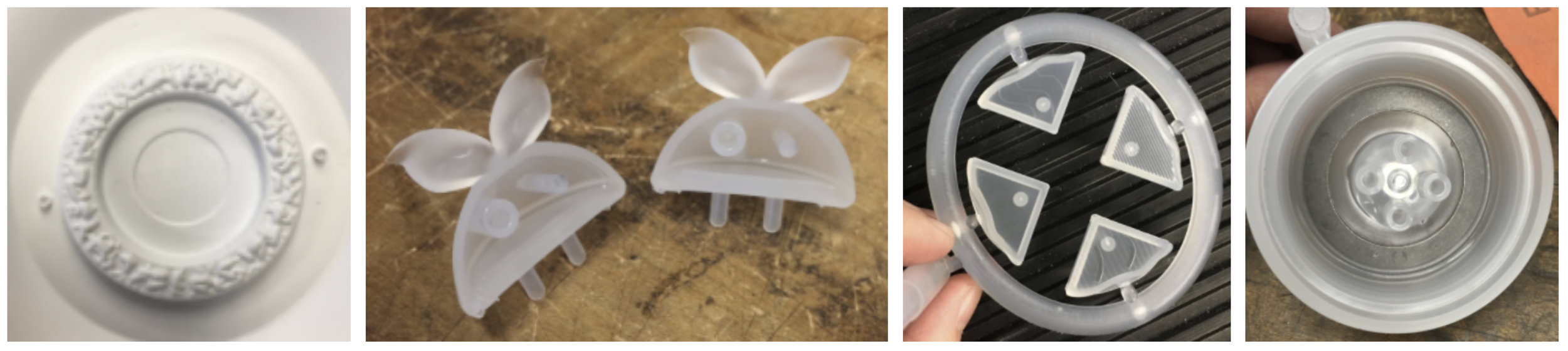

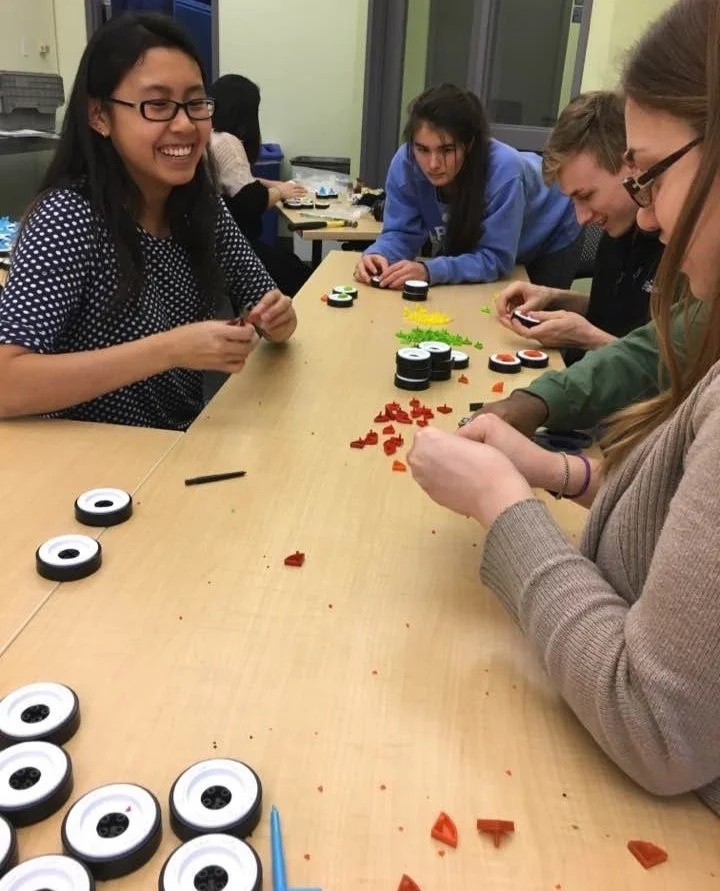
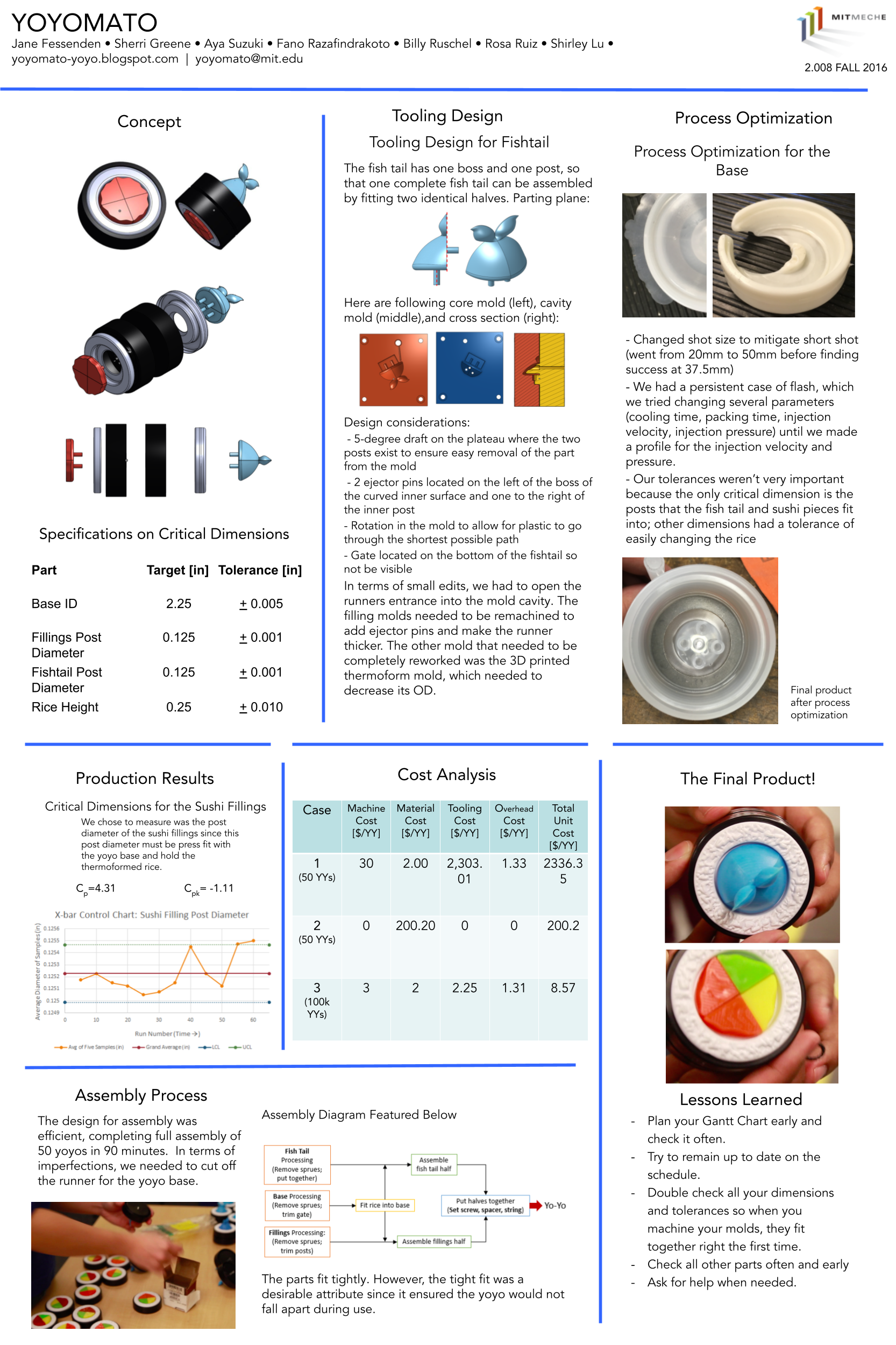